By Serena zhang | 05 June 2024 | 0 Comments
How to Calibrate 5-Axis CNC Router - a Detailed Guide with Letters and Videos
Axis CNC Router calibration has included two aspects: hardware and software.
1. In terms of hardware, it mainly involves the assembly of machine tools and the calibration of X/Y/Z/B/C axis and RTCP calibration;
2. Software calibration, corresponding parameter settings need to be made based on cutting tools, processing materials, and processing forms etc.
Preparation work before calibration
Tools :

Inspection rod
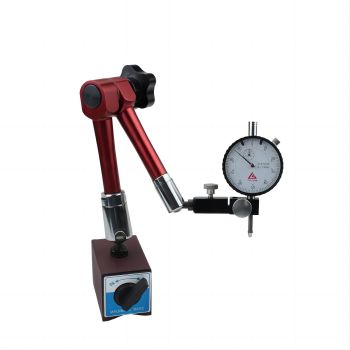
Dial indicator
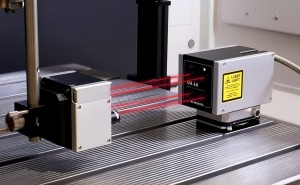
Laser device
5 AXIS CNC ROUTER HARDWAR Calibration Process :
1. Firstly, it is necessary to ensure that the machine is assembled correctly to avoid excessive vibration and deviation from the machine body. That need engineers install the gear wheel touch rack tightly and you should push the X Y Z axis hy hand to check there is gap between gear wheel and rack pinion.
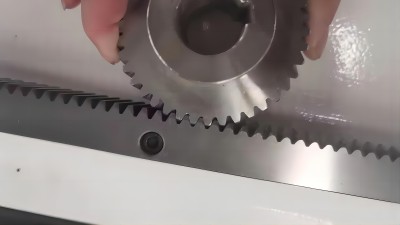
Because inside of machine program all parameters are set well as per machine assembled status like the strength and rigidy etc.
2. Diagonal adjustment :
In the diagonal inspection, usually we will mark 4 points along with machine table biggest size .
For example the table size 2000mmx3000mm, we will mark 4 points along with 2000mm and 3000mm. Then measure the diagonal length same or not .The error should less 0.01mm .
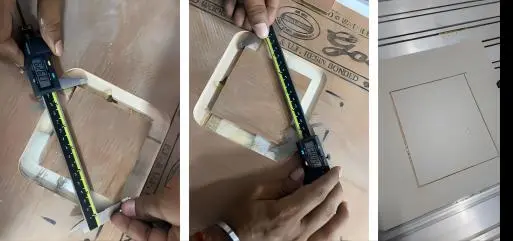
3. After completing the Diagonal adjustment, it is necessary to set the coordinate system of the machine tool to determine the origin and angle of the coordinate system,like machine basic X/Y/Z three axis setup.
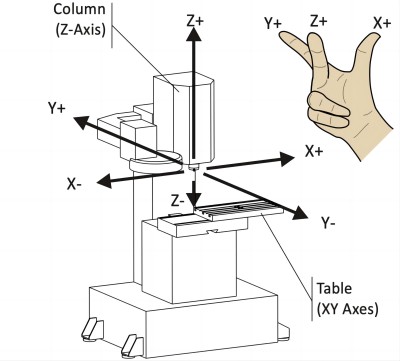
4. The most RTCP function in 5 axis cnc milling center calibation :
Firstly, it is necessary to calibrate the positioning accuracy and repeated positioning accuracy of this 5 axis cnc machine. If the positioning accuracy and repeated positioning accuracy of the machine tool are not properly calibrated and exceed the accuracy standards of the machine tool, the various coordinate axes of the machine tool will not be able to accurately compensate for displacement during RTCP motion, resulting in displacement of the tool center and errors in RTCP. The positioning accuracy and repetitive positioning accuracy of the machine tool can be corrected using a laser interferometer according to relevant detection standards (such as the JIS standard or ISO standard of VDI DGQ3441 in Germany), so that the positioning accuracy of each axis and repetitive positioning accuracy are within the accuracy standard range of the 5 axis cnc router, and the smaller the better.
Secondly, it is necessary to calibrate the absolute zero position of the machine tool's return axis (B C Axis). The method for calibrating the absolute zero position of the B-axis is shown in the following figure. After installing the relevant instruments, turn off the RTCP function, move the Z-axis with a handwheel, detect the deviation of the A-axis (at this point, the B-axis is at the zero position), and add the detected error to the system's return to zero preset value parameter AXSZPR (AM). After compensation, return the B-axis to zero, retest the zero point deviation of B, and repeatedly compensate until the zero point deviation of the B-axis meets the accuracy standard requirements
Below is the detail operation video for your reference:
https://youtu.be/H9coKhprKMk
The basic is B and C axis setting because before machine delivery at factory we already set RTCP well. When you receive you only need set again the B and C axis home point then ok .
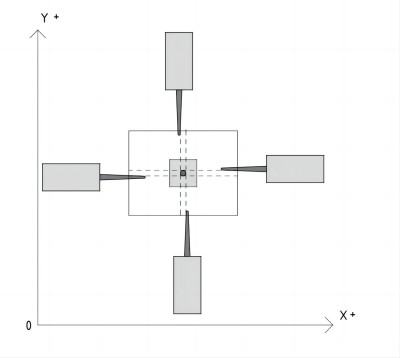
There need the inspection rod and Dial indicator to assist you finish this work well.
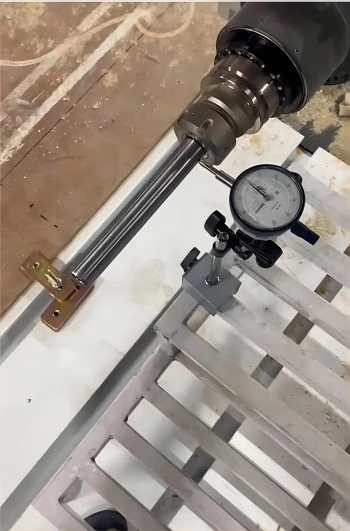
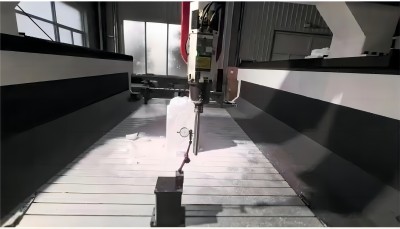
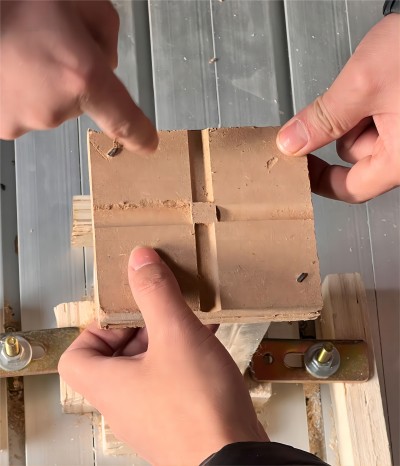
5 Axis CNC Router Progrom and software calibration
The programming of a five axis engraving machine requires the configuration of parameters such as tool radius, cutting depth, and cutting speed, as well as the setting of machining paths, starting points, and ending points.
In the programming process, it is necessary to use corresponding tools and materials, as well as suitable machining methods, in order to ensure the machining effect.
When programming, the first step is to select the correct CAD software, use 3D design software for model design and generation, and then import the model into CAM software to generate G codes that meet the requirements of machine tool processing. In the process of generating G code, it is necessary to pay attention to the reasonable setting of the machining path, taking into account factors such as tool entry and exit, corner transition, etc., in order to ensure machining accuracy and surface smoothness.
Usually we use PowerMill 2024 for design and postprocesser for G-CODE created
Overall, cablication and programming of a five axis cnc router machine is not very difficult. It only requires operating according to the relevant steps and processes, which requires patience and attention from beginners.
At the same time, it is necessary to pay attention to the selection of appropriate hardware and software , as well as the selection of tool materials and the configuration of machining parameters, in order to ensure machining quality and efficiency.
Some popular 5 axis ready calibration cnc router recommended:
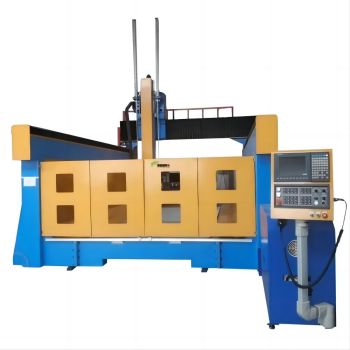
Italy Hiteco 17kw 3D 5 Axis Milling Machine for Yacht Boat Car Aircraft Molds on Wood Fiberglass Composite EPS Foam Plastic
China 1325 Table Moving 5 Axis CNC Router Machining Center for Woodworking Model Sculpture Statue
China Rhino 1300mmx2500mm large single table moving 5 axis cnc router machining center is the most popular model machine in market with cheap price and high quality working performance.
4x8ft large table moving with z axis 1000mm that have multi function

EPS Wood Foam Fiber Glass 5 Axis CNC Router Machining Center for Boat Mockup Car Yacht Plug Aircraft model Making
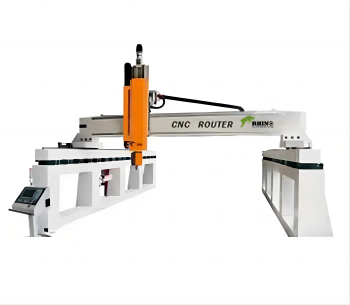
Precision 5-Axis CNC Router for Advanced Mold Making & Sculpting
Discover the ultimate in precision with RhinoCNC's 5-Axis CNC Router. Ideal for mold making and sculpting, our CNC router transforms complex designs into reality with unparalleled accuracy. Explore the perfect tool for foam, car, aluminum, and boat molds
The end ...
1. In terms of hardware, it mainly involves the assembly of machine tools and the calibration of X/Y/Z/B/C axis and RTCP calibration;
2. Software calibration, corresponding parameter settings need to be made based on cutting tools, processing materials, and processing forms etc.
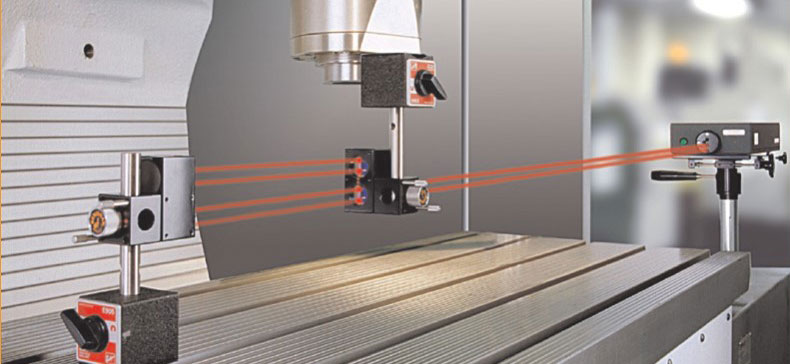
Preparation work before calibration
Tools :

Inspection rod
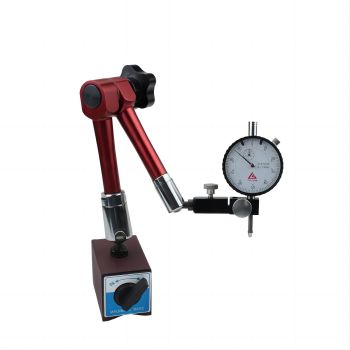
Dial indicator
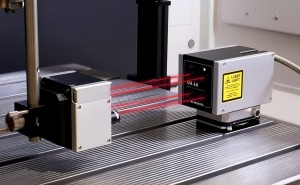
Laser device
5 AXIS CNC ROUTER HARDWAR Calibration Process :
1. Firstly, it is necessary to ensure that the machine is assembled correctly to avoid excessive vibration and deviation from the machine body. That need engineers install the gear wheel touch rack tightly and you should push the X Y Z axis hy hand to check there is gap between gear wheel and rack pinion.
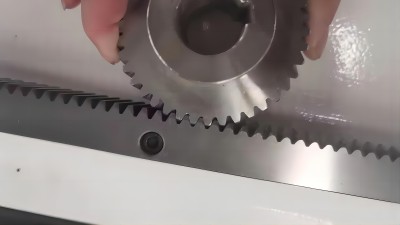
Because inside of machine program all parameters are set well as per machine assembled status like the strength and rigidy etc.
2. Diagonal adjustment :
In the diagonal inspection, usually we will mark 4 points along with machine table biggest size .
For example the table size 2000mmx3000mm, we will mark 4 points along with 2000mm and 3000mm. Then measure the diagonal length same or not .The error should less 0.01mm .
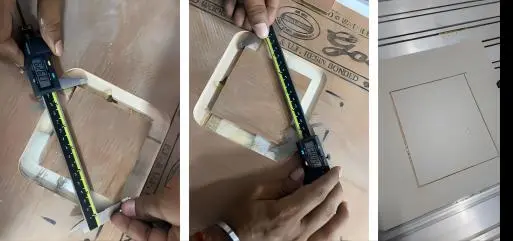
3. After completing the Diagonal adjustment, it is necessary to set the coordinate system of the machine tool to determine the origin and angle of the coordinate system,like machine basic X/Y/Z three axis setup.
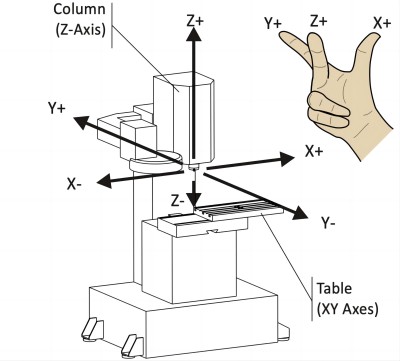
4. The most RTCP function in 5 axis cnc milling center calibation :
Firstly, it is necessary to calibrate the positioning accuracy and repeated positioning accuracy of this 5 axis cnc machine. If the positioning accuracy and repeated positioning accuracy of the machine tool are not properly calibrated and exceed the accuracy standards of the machine tool, the various coordinate axes of the machine tool will not be able to accurately compensate for displacement during RTCP motion, resulting in displacement of the tool center and errors in RTCP. The positioning accuracy and repetitive positioning accuracy of the machine tool can be corrected using a laser interferometer according to relevant detection standards (such as the JIS standard or ISO standard of VDI DGQ3441 in Germany), so that the positioning accuracy of each axis and repetitive positioning accuracy are within the accuracy standard range of the 5 axis cnc router, and the smaller the better.
Secondly, it is necessary to calibrate the absolute zero position of the machine tool's return axis (B C Axis). The method for calibrating the absolute zero position of the B-axis is shown in the following figure. After installing the relevant instruments, turn off the RTCP function, move the Z-axis with a handwheel, detect the deviation of the A-axis (at this point, the B-axis is at the zero position), and add the detected error to the system's return to zero preset value parameter AXSZPR (AM). After compensation, return the B-axis to zero, retest the zero point deviation of B, and repeatedly compensate until the zero point deviation of the B-axis meets the accuracy standard requirements
Below is the detail operation video for your reference:
https://youtu.be/H9coKhprKMk
The basic is B and C axis setting because before machine delivery at factory we already set RTCP well. When you receive you only need set again the B and C axis home point then ok .
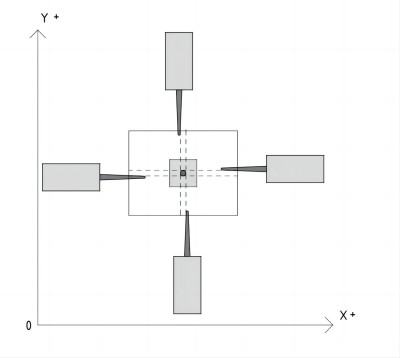
There need the inspection rod and Dial indicator to assist you finish this work well.
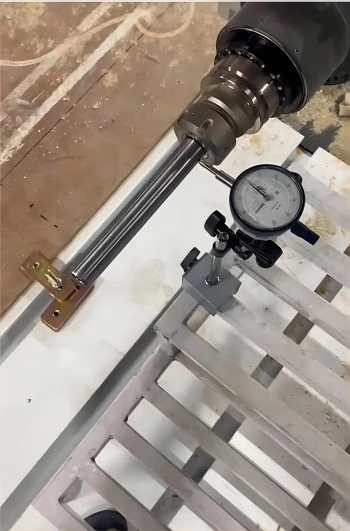
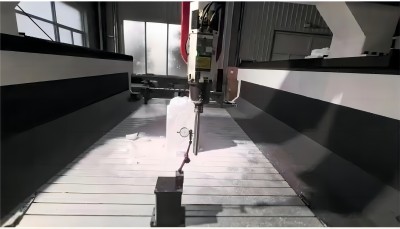
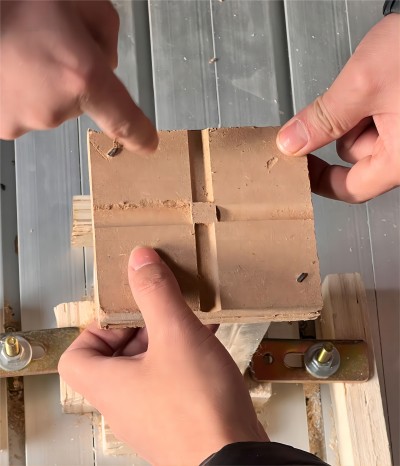
5 Axis CNC Router Progrom and software calibration
The programming of a five axis engraving machine requires the configuration of parameters such as tool radius, cutting depth, and cutting speed, as well as the setting of machining paths, starting points, and ending points.
In the programming process, it is necessary to use corresponding tools and materials, as well as suitable machining methods, in order to ensure the machining effect.
When programming, the first step is to select the correct CAD software, use 3D design software for model design and generation, and then import the model into CAM software to generate G codes that meet the requirements of machine tool processing. In the process of generating G code, it is necessary to pay attention to the reasonable setting of the machining path, taking into account factors such as tool entry and exit, corner transition, etc., in order to ensure machining accuracy and surface smoothness.
Usually we use PowerMill 2024 for design and postprocesser for G-CODE created
Overall, cablication and programming of a five axis cnc router machine is not very difficult. It only requires operating according to the relevant steps and processes, which requires patience and attention from beginners.
At the same time, it is necessary to pay attention to the selection of appropriate hardware and software , as well as the selection of tool materials and the configuration of machining parameters, in order to ensure machining quality and efficiency.
Some popular 5 axis ready calibration cnc router recommended:
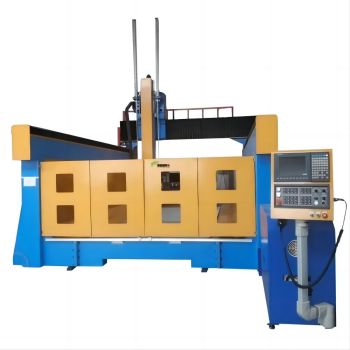
Italy Hiteco 17kw 3D 5 Axis Milling Machine for Yacht Boat Car Aircraft Molds on Wood Fiberglass Composite EPS Foam Plastic
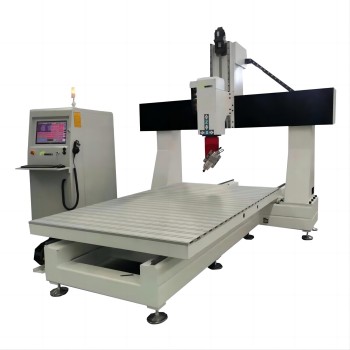
China 1325 Table Moving 5 Axis CNC Router Machining Center for Woodworking Model Sculpture Statue
China Rhino 1300mmx2500mm large single table moving 5 axis cnc router machining center is the most popular model machine in market with cheap price and high quality working performance.
4x8ft large table moving with z axis 1000mm that have multi function

EPS Wood Foam Fiber Glass 5 Axis CNC Router Machining Center for Boat Mockup Car Yacht Plug Aircraft model Making
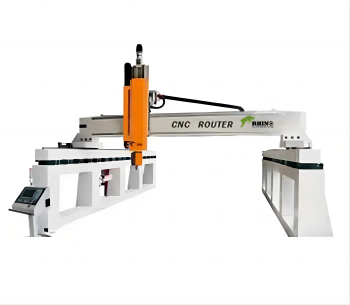
Precision 5-Axis CNC Router for Advanced Mold Making & Sculpting
Discover the ultimate in precision with RhinoCNC's 5-Axis CNC Router. Ideal for mold making and sculpting, our CNC router transforms complex designs into reality with unparalleled accuracy. Explore the perfect tool for foam, car, aluminum, and boat molds
The end ...
Leave a Reply
Your email address will not be published.Required fields are marked. *
POPULAR BLOG